Case Study: RobSimulation for robot programming of steering column switch measurements
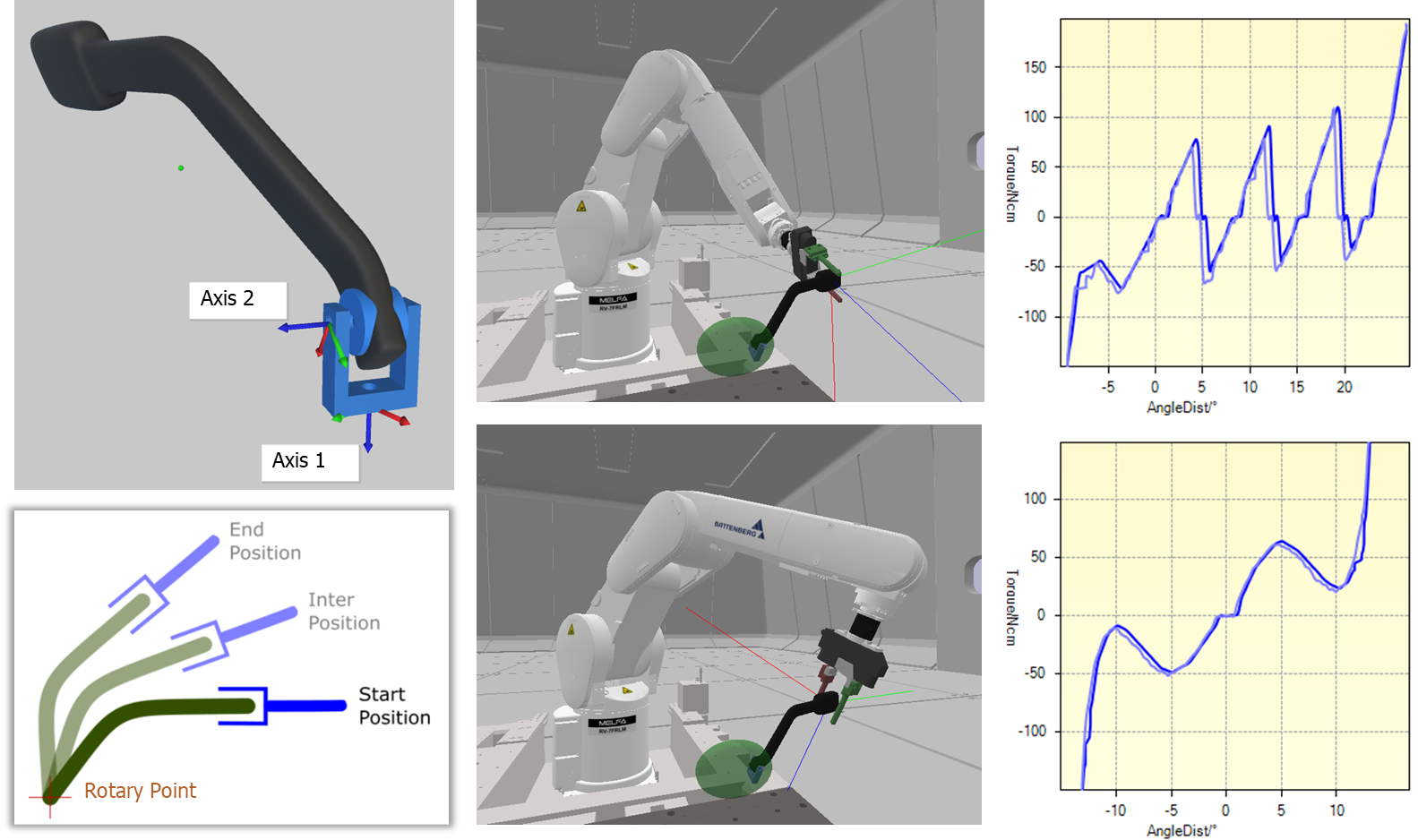
Offlineprogramming using RobSimulation is already being used successfully and efficiently by customers. For example, a setup for testing the haptic quality of a steering column switch has been realised:
The measurement task consists of actuating a steering column switch (e.g. indicator lever) with two axes and testing the haptics and function (CAN, LIN). This rotational movement around two axes requires a robot with a 3D force sensor on the hand, which grips the lever at a defined position and moves it along the circular path around the hidden axis: this is the only way to record the pure operating forces and torques without artefacts such as forces caused by tilting of the tool and lever.
In RobSimulation, the CAD model of the steering column switch can be used to determine the axes around which the robot hand with force sensor must move the switch in order to confirm it correctly. The orientation of the actuating tool is also not arbitrary if forces are to be measured tangentially to the axis movement: This information can also be defined on the CAD model. In addition, a force or torque curve is stored in RobSimulation for each axis, as well as axis limits.
The virtual robot actuates the steering column switch in RobSimulation, with the lever following and producing virtual force readings that are recorded by the virtual force sensor. The entire robot movement can be viewed in advance and checked for reachability before moving onto the real steering column switch. After a short (haptic) calibration process, the robot paths from RobSimulation are transferred to the real robot, which actuates the steering column switch correctly - as defined in RobSimulation.
This ensures that the operating forces, frequencies and test positions correspond to the customer specifications.
Using CAD data and the desired measuring positions, the measuring cell could be set up virtually at Battenberg and the measuring sequence created according to customer specifications. The measurement task could then be transferred to the real robot at the customer's premises and the quality inspection carried out directly.
Virtual commissioning can be carried out either as a Battenberg service or entirely on the customer's premises.
Case Study: RobSimulation for robot programming of steering column switch measurements
signup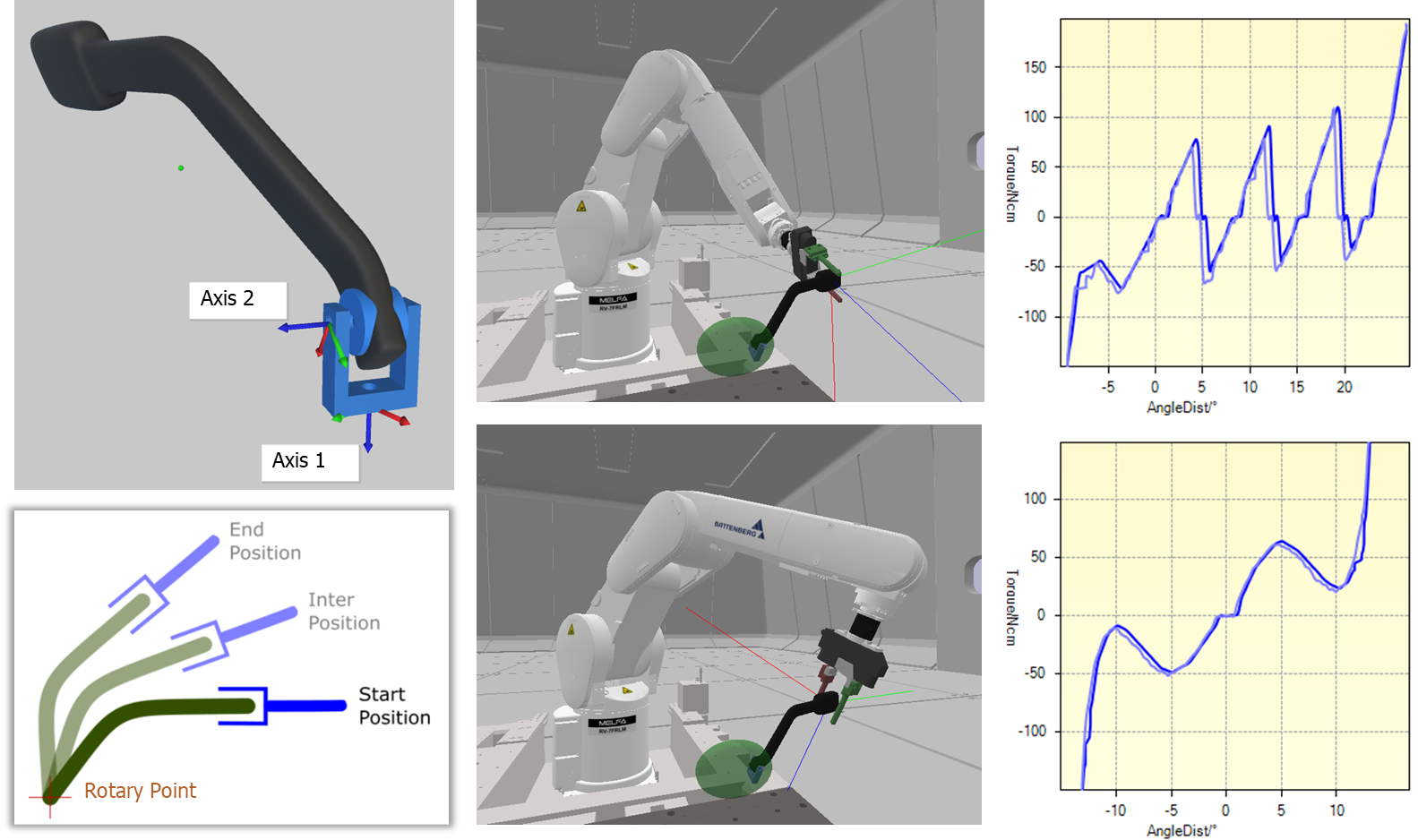
Offlineprogramming using RobSimulation is already being used successfully and efficiently by customers. For example, a setup for testing the haptic quality of a steering column switch has been realised:
The measurement task consists of actuating a steering column switch (e.g. indicator lever) with two axes and testing the haptics and function (CAN, LIN). This rotational movement around two axes requires a robot with a 3D force sensor on the hand, which grips the lever at a defined position and moves it along the circular path around the hidden axis: this is the only way to record the pure operating forces and torques without artefacts such as forces caused by tilting of the tool and lever.
In RobSimulation, the CAD model of the steering column switch can be used to determine the axes around which the robot hand with force sensor must move the switch in order to confirm it correctly. The orientation of the actuating tool is also not arbitrary if forces are to be measured tangentially to the axis movement: This information can also be defined on the CAD model. In addition, a force or torque curve is stored in RobSimulation for each axis, as well as axis limits.
The virtual robot actuates the steering column switch in RobSimulation, with the lever following and producing virtual force readings that are recorded by the virtual force sensor. The entire robot movement can be viewed in advance and checked for reachability before moving onto the real steering column switch. After a short (haptic) calibration process, the robot paths from RobSimulation are transferred to the real robot, which actuates the steering column switch correctly - as defined in RobSimulation.
This ensures that the operating forces, frequencies and test positions correspond to the customer specifications.
Using CAD data and the desired measuring positions, the measuring cell could be set up virtually at Battenberg and the measuring sequence created according to customer specifications. The measurement task could then be transferred to the real robot at the customer's premises and the quality inspection carried out directly.
Virtual commissioning can be carried out either as a Battenberg service or entirely on the customer's premises.
Event registration
Please feel free to contact us to register for the event. After verifying your contact details, we will be happy to send you further information on how to register.
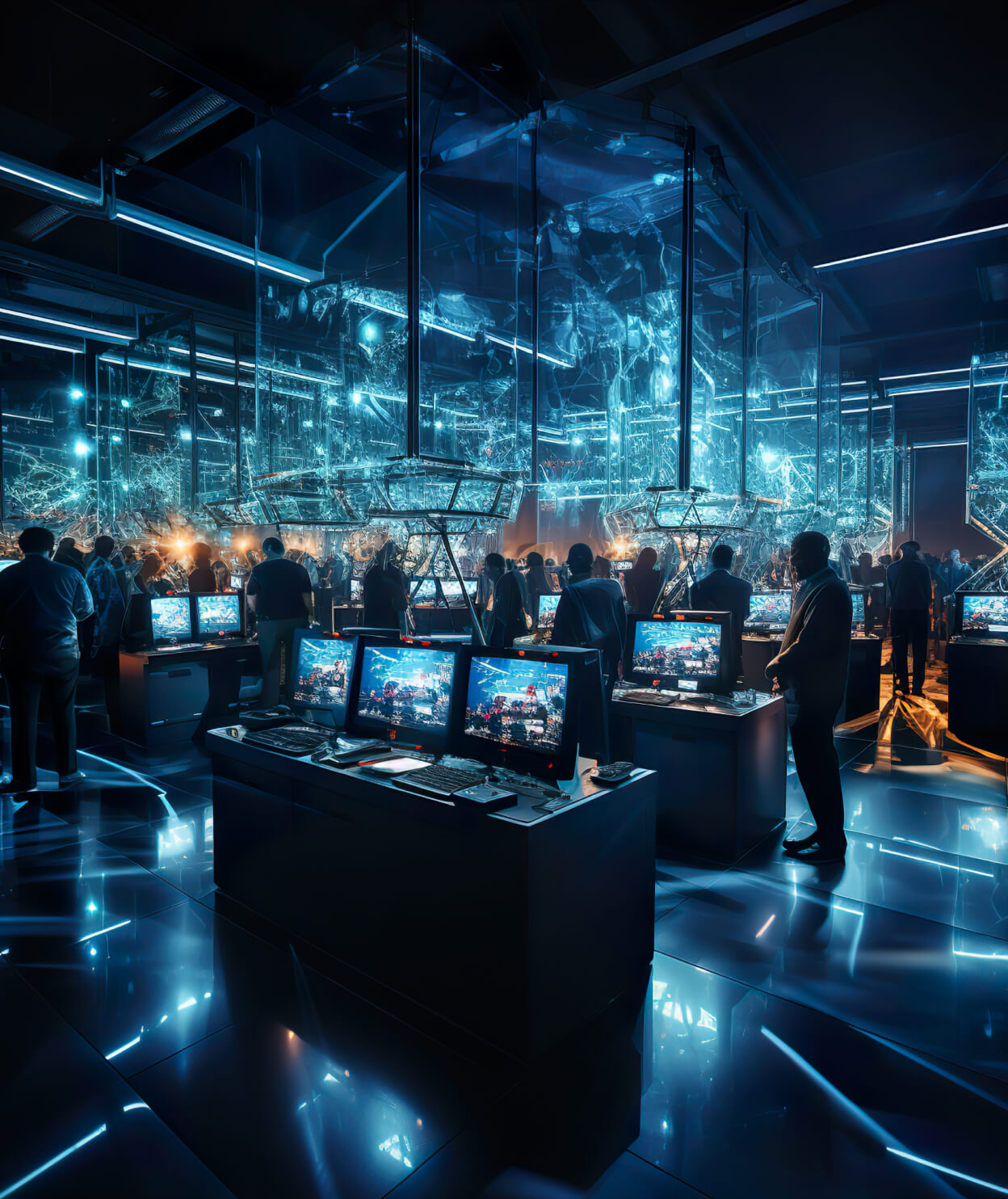